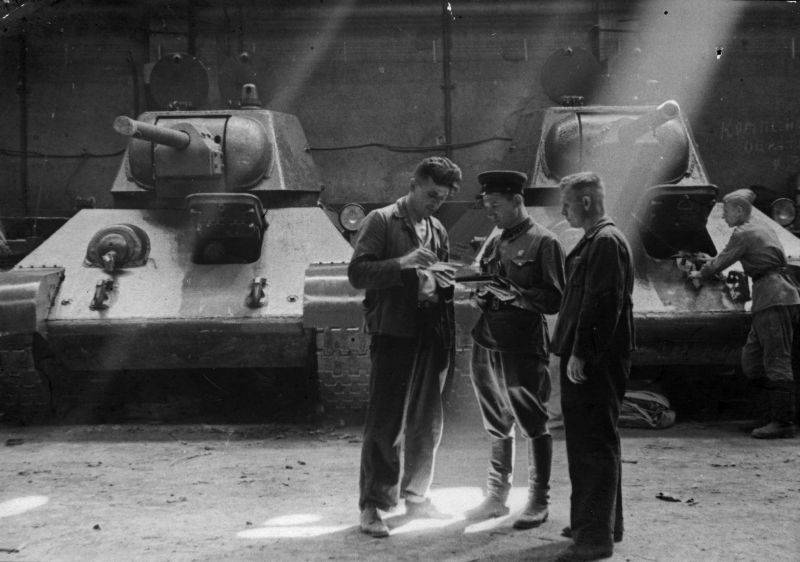
Приемка танков Т-34, сошедших с конвейера завода № 183 в Нижнем Тагиле. Источник: waralbum.ru
Все на войну с трещиной!
Высокотвердая гомогенная бронесталь 8С, ставшая основной для среднего танка Т-34, привнесла немало сложностей в технологический процесс производства. Надо отметить, что столь твердая броня в период всей Второй мировой войны на танках применялась только в Советском Союзе. И в этом, безусловно, были как положительные, так и отрицательные стороны. В предыдущих частях цикла уже шла речь о многочисленных трещинах, сопровождающих сварку корпусов и башен средних советских танков. При этом тяжелые КВ и затем ИСы были лишены этого: более пластичная броня средней твердости гораздо легче переносила избыточные напряжения при сваривании деталей. Инженеры «Броневого института» с начала 1942 года предложили комплекс мер по упрощению бронекорпусного производства и модернизации технологии сварки. Некоторые узлы вообще было решено не сваривать: к примеру, крепление задних и передних рам перевели на клёпку. Во многом это было заимствование после тщательного изучения немецких бронемашин.
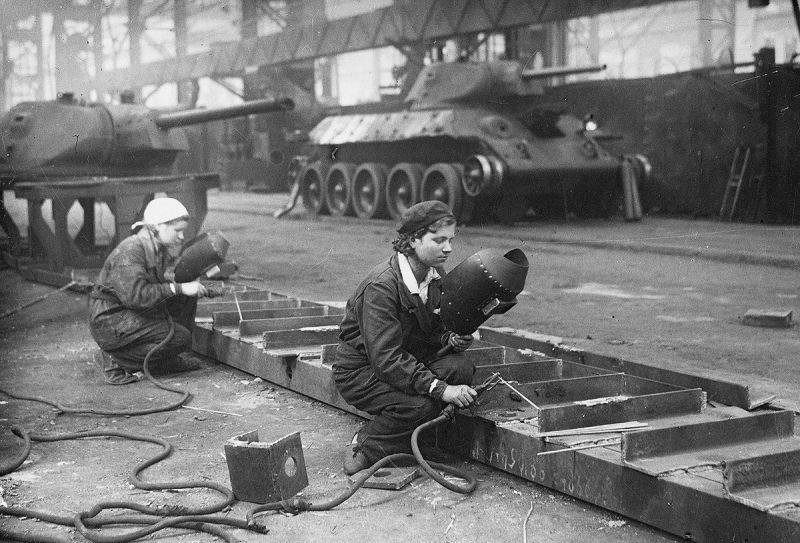
Женщины-сварщицы за работой на Уральском танковом заводе в цеху сборки танков Т-34. Источник: waralbum.ru
Лобовые и бортовые детали танка сваривались теперь по требованию ЦНИИ-48 только аустенитовыми электродами, лучше приспособленными для трудносвариваемых сортов черного металла. В общей сложности теперь до 10% (или более) всех электродов, расходуемых на бронемашину, были аустенитовыми. Если ориентироваться на данные, приведенные в книге Никиты Мельникова «Танковая промышленность СССР в годы Великой Отечественной войны», то на один Т-34-76 расходовали порядка 400 электродов, и 55 из них были аустенитовые. Среди требований к использованию подобных электродов был запрет на их работу при повышенных режимах токах – до 320А. Превышение этого показателя грозило высоким разогревом области шва с последующей деформацией при остывании и образованием трещин. Обратите внимание, что функции, подобные отечественному «Броневому институту», в Германии выполнял 6-й Департамент Управления вооружений сухопутных сил. Именно ему танковые заводы должны были представлять методы сварки корпусов и башен на утверждение в письменной форме. Спецы 6-го Департамента, в свою очередь, проверяли представленные материалы на соответствие временным техническим условиям сварки брони T.L.4014, T.L.4028 и T.L.4032. Данные требования были рассчитаны на сварку немецкой брони толщиной от 16 до 80 мм. Как уже говорилось в материале «Сварка танковой брони: немецкий опыт», в Германии не использовалась автоматическая сварка. Это, безусловно, серьезно тормозило скорость работы немецкой танковой отрасли, но и в Советском Союзе со сварочными автоматами были некоторые проблемы. Наряду с несомненным высоким качеством сварочного шва автоматизация сварки потребовала высококачественных присадочных материалов и строго соблюдения технологии работы. Однако это было неизбежной платой внедрение революционного метода производства, оказавшего столь значительное влиянием на качество и скорость сборки танков.
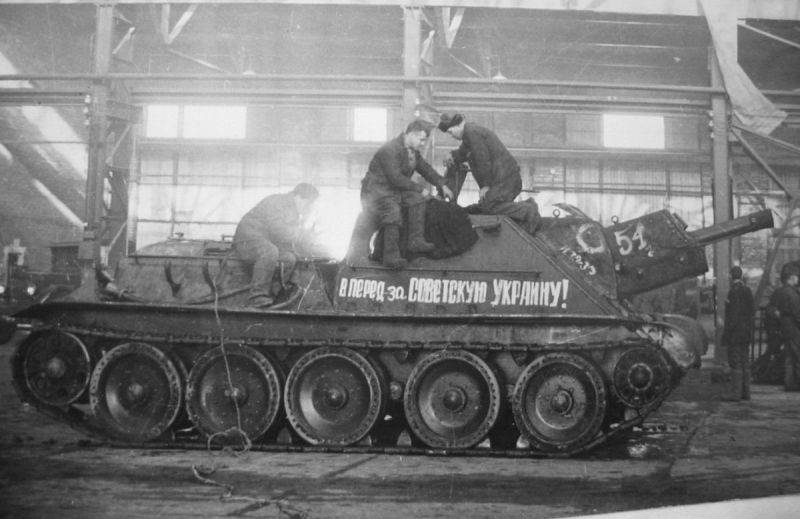
Рабочие свердловского завода за сборкой САУ СУ-122. Источник: waralbum.ru
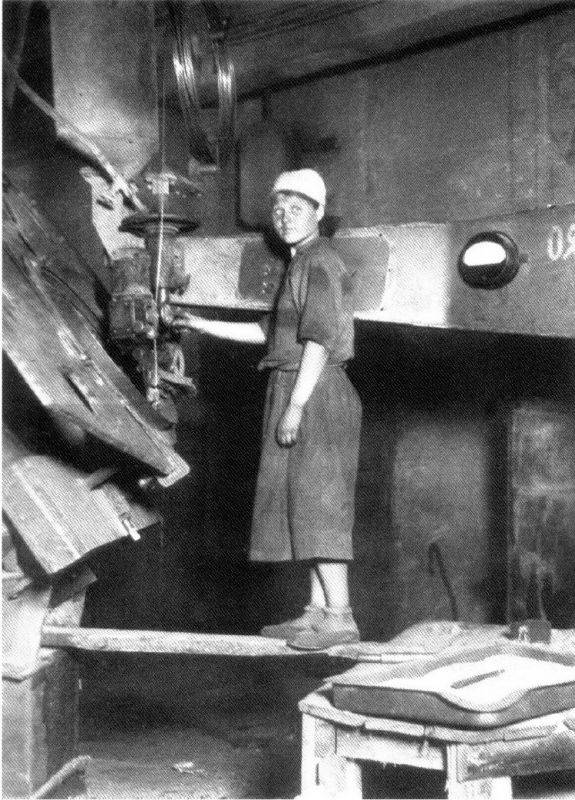
Приварка командирской башенки к крыше танковой башни Т-34-85 автоматической сварочной установкой на Уральском танковом заводе №183 в Нижнем Тагиле. Источник: waralbum.ru
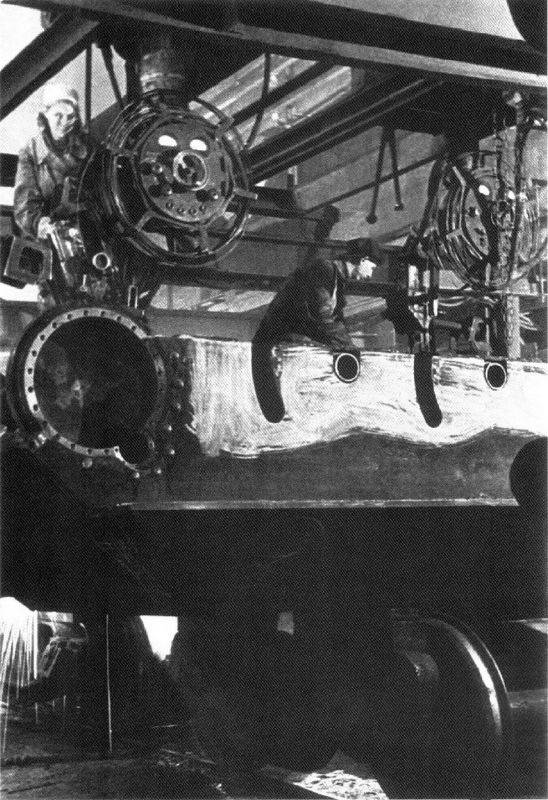
Сварка корпуса танка Т-34 автоматической сварочной установкой на Уральском танковом заводе №183 в Нижнем Тагиле. Источник: waralbum.ru
Если основная электродная и присадочная проволока оказывалась чрезмерно загрязнена серой, углеродом и фосфором (либо, наоборот, в ней недоставало марганца или оксида марганца), это приводило к образованию трещин непосредственно в сварочном шве. Важно было тщательно подготовить свариваемые изделия под флюс. Требования были жесткие: детали должны быть правильных размеров, без нарушений допусков. В ином случае для сваривания деталь на стапеле приходились «натягивать», тем самым создавая серьезные внутренние напряжения. Да и простое несоблюдение силы и напряжение сварочного тока приводило к дефективности швов: пористости, ноздреватости и непроварам. Учитывая низкий уровень квалификации рабочих, допускаемых до сварочных автоматов, в возможность брака такого рода верится легко. Все высококвалифицированные сварщики были заняты в ручной сварке и не могли влиять на качество сварки "машин Патона". Хотя их привлекали для исправления дефектов сварочных автоматов.
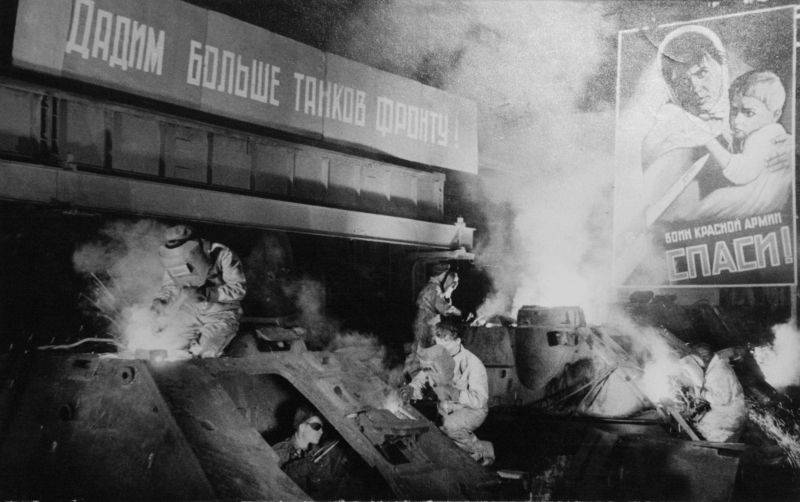
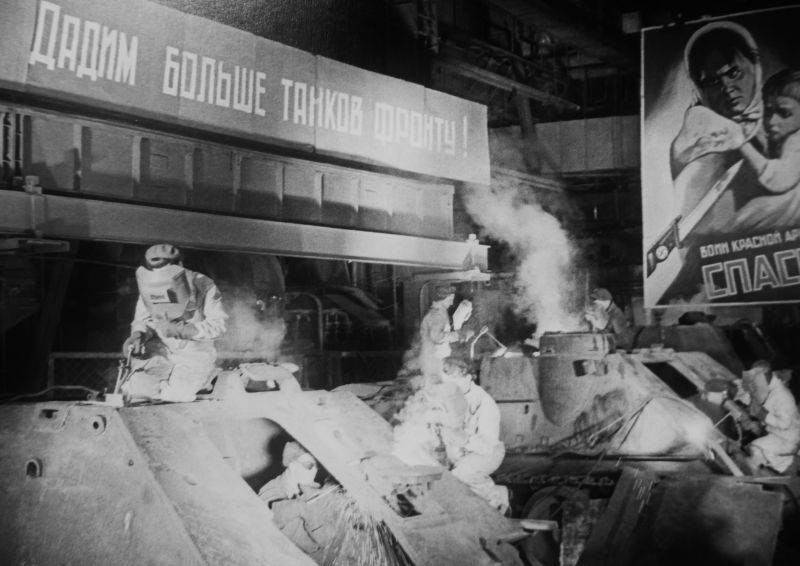
Сварка корпусов САУ СУ-122 и СУ-100 на Уральском заводе тяжелого машиностроения. Источник: waralbum.ru
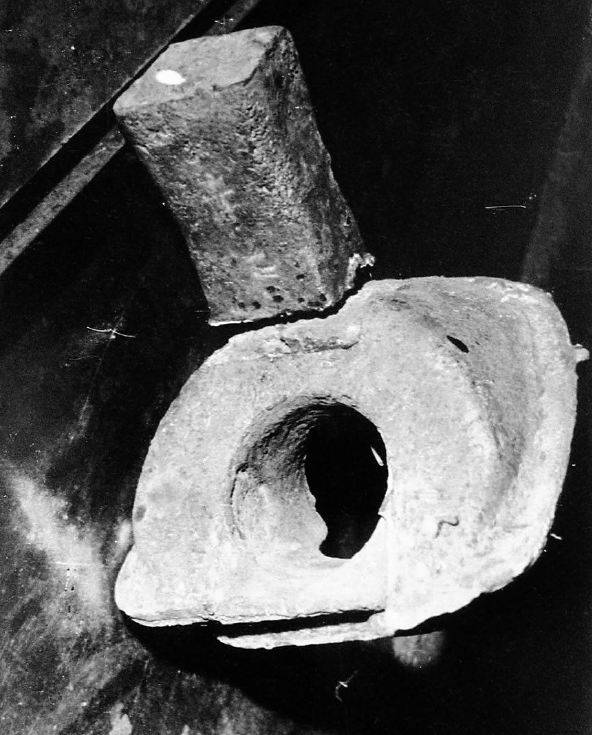
Литая деталь бронезащиты курсового пулемета ДТ. Завод № 183, 1942 год. Источник: Российский государственный архив экономики
Резкий рост производительности танковых заводов привел к 1943 году к одной неожиданной проблеме. Оказалось, что остальное производство не всегда успевало за танкостроением. Станки работали на износ, порой отсутствовали амперметры для контроля силы тока на автоматах, недоставало качественных сварочных электродов. Все это вызывало периодические «всплески» трещинообразования среди серийных Т-34. Гасить эти волны брака приходилось оперативными силами заводских технологов и инженеров из ЦНИИ-48.
Пересмотр конструкции
Твердая броня и трещины в ней заставили инженеров изменить не только технологию автоматической сварки, но и ручной подход. Большие сварочно-термические напряжения, в частности, испытывала верхняя лобовая деталь, когда на ней в процессе конвейерной сборки наваривали защиту пулемета ДТ, рымы, петлю водительского люка, защитную планку и другие мелочи. Вокруг защиты пулемета, которую очень тщательно обваривали, возникали нередко трещины длиной до 600 мм! Объемной была сварка в районе носовой части бортов, где они скреплялись мощными двухсторонними швами с лобовой верхней и нижней плитами, а также с кронштейнами ленивца. Часто зазор между деталями в данных частях не соответствовал нормативным и поэтому приходилось класть особенно массивный сварочный шов, оставляющий после себя серьезные внутренние напряжения. Требовалось уменьшить жесткость некоторых узлов и снизить общую долю сварки в соединениях, что и было сделано специалистами ЦНИИ-48 в самое кратчайшее время. В частности, изменили способ соединения подкрылков с передней деталью крыши корпуса. С помощью специальной «буферной» планки из малоуглеродистой стали, которую предварительно приваривали к подкрылку, удалось снизить уровень итогового напряжения внутри шва и брони вокруг. Далее разобрались с упоминаемой «инфраструктурой» на лобовой плите танка. Теперь приваривать рымы, защиту пулемета и петли люка по новым техническим условиям можно было только 5-6-мм электродами несколькими слоями: не менее четырех! Аналогичным способом соединяли подкрылки с крышей, лобовую плиту с бортами, подкрылками и крышей. Все остальное варили в 2-3 захода с 7-10-мм электродами.
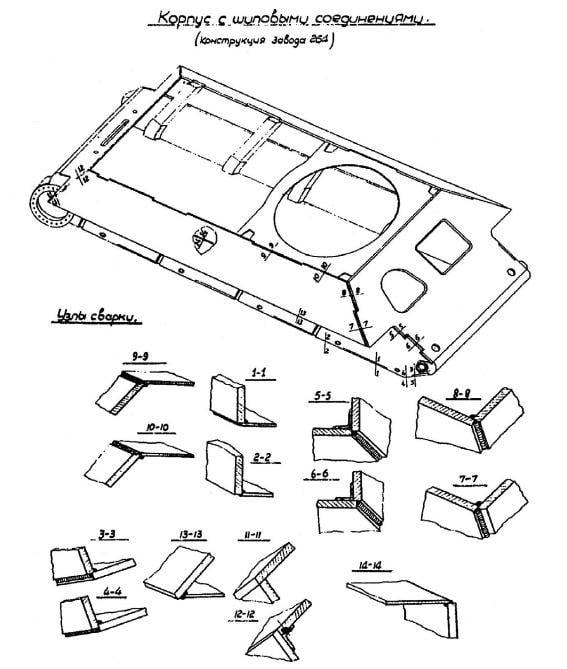
Источник: Российский государственный архив экономики
Изменили и технологию соединений деталей корпуса танка Т-34. Первоначально все соединения, кроме сопряжения ВЛД и НЛД, были как по чертежам выполнены в четверть. Но вскоре после начала войны их поменяли на шиповое, но и оно себя не оправдало – слишком много появилось трещин в местах вырезания швов. Шиповое соединение для высокотвердой брони было не совсем уместно также по причине сильных местных усадочных напряжений после сварки. Что было хорошо пластичной немецкой броне, для отечественных Т-34 не подходило. Только в 1943 году на «танке победы» появились окончательные варианты сочленения, удовлетворившие специалистов ЦНИИ-48 – внахлестку и впритык.
Танковый корпус на кантователе. Источник: Российский государственный архив экономики
Проще всего процессы оптимизации сварочных работ прошли корпуса тяжелых советских танков. Соединение бронеплит в четверть на КВ оставили без изменений, но вот внутренние усилительные угольники заменили внутренними угловыми швами. Уже в самый разгар войны для тяжелых танков были выбраны (снарядными обстрелами прежде всего) наиболее оптимальные конфигурации сопряжения бронеплит. Если угол соединения был близок к 90 градусам, то лучше было использовать метод «в шип» или в четверть, а во всех остальных вариантах – враспор или в зуб. По итогам этих исследований в ЦНИИ-48 родилась своеобразная форма верхней части носового узла танка ИС-2, когда при толщине 100-110 мм броня обеспечивала всеракурсную защиту от снарядов 88-105 мм. Сопряжение деталей в этой прочной конструкции было простым, враспор.
Немає коментарів:
Дописати коментар