Нью-Йорк, 2008 год, Падение крана
«Исследователи, которые изучали обстоятельства падения крана, выяснили, что причиной катастрофы стал дефект в детали, которая недавно была восстановлена»
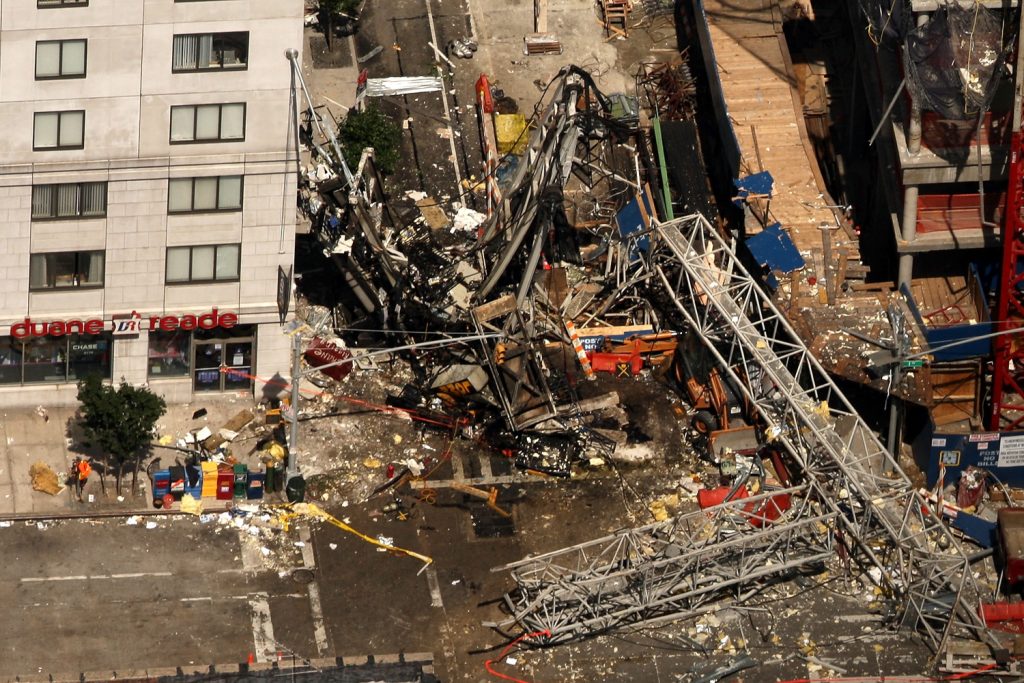
Разрушения, которые нанес кран при падении
Дефект был обнаружен в сварном шве поворотной платформы крана, благодаря которой и происходит изменение направления движения. Деталь была отправлена на ремонт всего за несколько месяцев до катастрофы. Причиной падения крана стало разрушение ремонтного шва в этой детали.
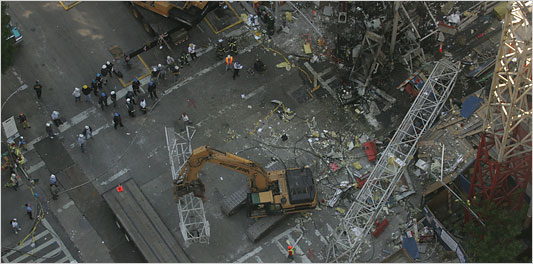
В результате этой катастрофы обвалилась 60 метровая часть крана. Значительных жертв удалось избежать, погибли два работника, (один из них работал на этом кране, другой — попал под обломки крана при его падении).
Хьюстон (штат Техас) 2004, Взрыв на фабрике по переработке нефтепродуктов
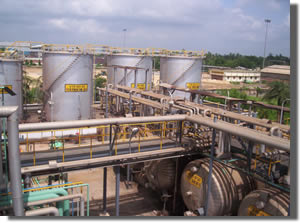
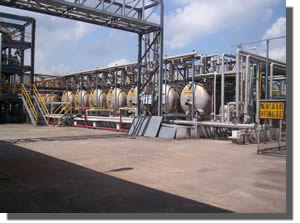
«Следователи CSB (Сhemical safety and hazard investigation board) [перевод. Комисия по химической безопасности] установили, что взрыв, который произошел на данном объекте произошел из-за ненадлежащего качества сварного шва при модернизации хранилища высокого давления №7»
Трагедия произошла в декабре 2004 года, в городе Хьюстон (Техас) на фабрике Marcus Oil facility, которая занимается переработкой полиэтиленовых восков для промышленного использования. В баке, который взорвался, находились неочищенные парафины, которые являются побочным продуктом производства.
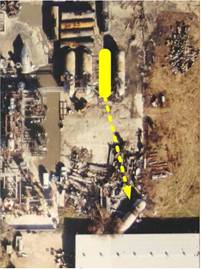
Перемещение резервуара, который взорвался
По неизвестным причинам произошел взрыв одного из хранилищ высокого давления, в котором хранились необработанные продукты нефтехимической промышленности. Сначала прогремел взрыв, тогда начался очень сильный пожар, который удалось затушить только спустя 12 часов. Несколько жителей были ранены в результате ранения осколками, которые разлетелись более чем на 500 метров. Во многих окрестных домах и автомобилях вылетели стекла. В результате пожара была практически полностью уничтожена фабрика Marcus Oil facility, сгорело 50000 фунтов (22700 кг) нефтепродуктов.
В ходе расследования CSB было выяснено, что взорвалось хранилище высокого давления №7. Незадолго до этого, данный сосуд проходил модернизацию, а именно установку нагревательных катушек. После этой модернизации необходимо герметизировать сосуд, путем приварки временной стальной пластины над техническим отверстием. Следствие выяснило, что ремонтные швы не соответствовали принятым стандартам качества для хранилищ высокого давления. Владелец фабрики грубо нарушил технику безопасности, наняв неквалифицированного сварщика, который выполнил шов ненадлежащего качества (не было выполнено скоса кромок, поэтому произошел значительный непровар. Также была замечена концентрация пор в шве, что абсолютно недопустимо для резервуаров, работающих под давлением). Также было выяснено, что никаких проверок после работ не было проведено, резервуар сразу был пущен в работу. Именно из-за разрушения шва между пластиной и временным отверстием и произошел взрыв. Механические характеристики (прочность и жесткость) сварного соединения были в четыре раза меньше, чем минимально допустимые для такого класса оборудования.
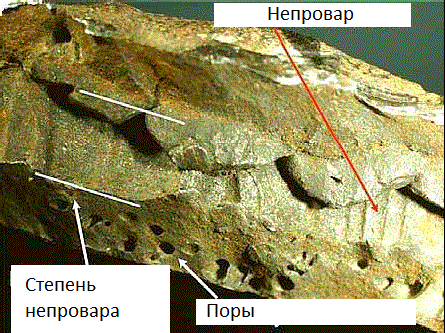
Разрез шва, который стал причиной катастрофы
Берингово море (у берегов Аляски) Декабрь 2004, Разлом корабля MV Selendang Ayu, экологическая катастрофа
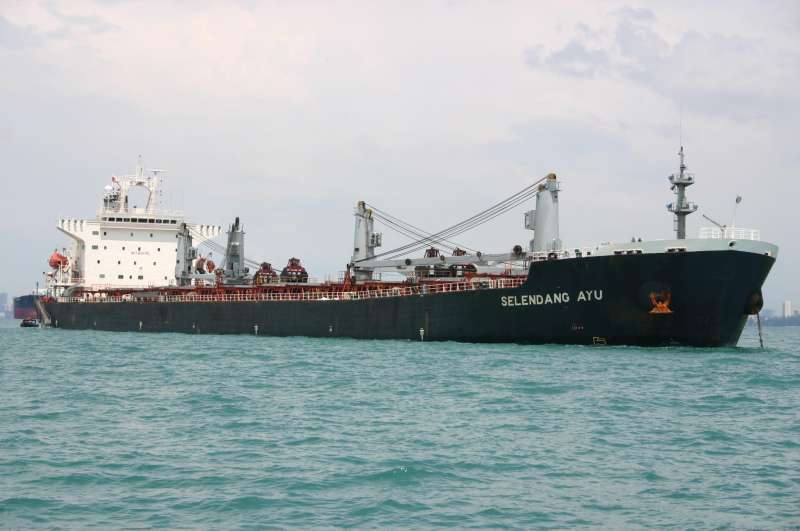
28 ноября 2004 Selendang Ayu покинул Сиэтл, Вашингтон, направляясь в Сямэнь, Китай. На борту находился груз 60,200 тонн соевых бобов, а также 1000 тонн мазута. Прибытие в Китай был назначено на 17 декабря, но из-за сильных штормов судно шло на тихом ходу, поэтому прибытие переносилось.
После того, как корабль прошел через пролив Unimak, у судна появились значительные неполадки двигателя, поэтому его было решено отключить. На тот момент судно находилось на 46 миль (74 км) к юго-западу от острова Bogoslof и около 100 миль (160 км) от порта Dutch Harbor.
Было установлено, что причиной отказа двигателя являлась трещина во вкладыше третьего цилиндра, поэтому инженеры корабля решили изолировать этот цилиндр, перезапустить двигатель, используя пять оставшихся цилиндров и отойти к гавани, где можно было бы отремонтировать дефектный цилиндр. Однако после изоляции цилиндра двигатель запустить не удалось. Шквальный ветер (8 по шкале Бофорта) относил корабль в сторону берега со скоростью 3 км / ч. Не смотря на все усилия, с утра двигатель не запустился на 5 цилиндрах, поскольку оказалось, что 4 из них были сильно повреждены (трещины в поршнях).
За несколько дней, которые корабль пробыл в свободном дрейфе, он успел приблизиться к мели. Попытки оттянуть корабль буксиром терпели неудачу, поскольку буксир не мог преодолеть силы волн (высотой до 7.6 метров).
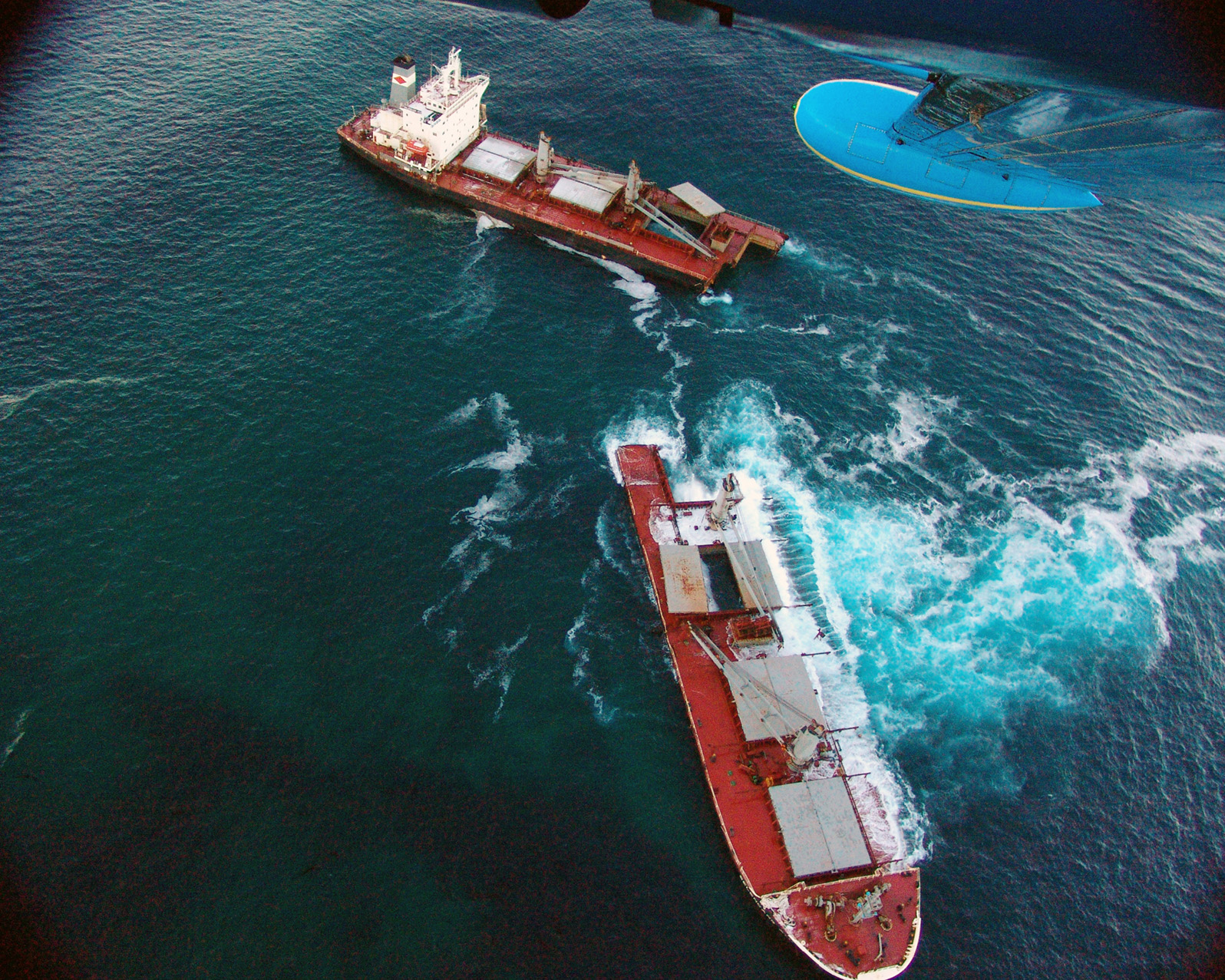
На помощь кораблю было отправлено 2 спасательных вертолета, один из которых затонул. В процессе подъема команды на борт вертолета, от сильного удара волны, корабль, который уже сидел на мели, было разломан пополам. 6 членов экипажа, находившихся на нем найти не удалось.
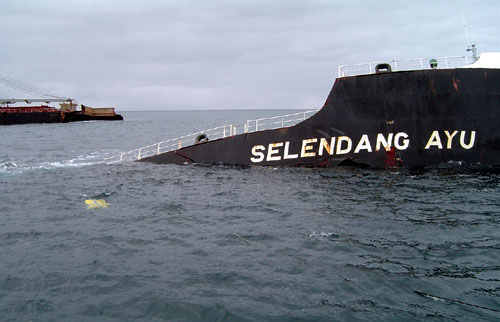
В этом случае сварка не являлась причиной катастрофы, но поскольку корабль, находясь на мели сломался (именно по швам), некачественные швы можно обвинить в экологической катастрофе, поскольку при разломе корабля в море было выброшено около 900т нефтепродуктов. Эксперты отметили, что в процессе постройки корабль не проходил надлежащий контроль сварных швов.
Мексиканский залив (штат Луизиана) 2005, Падение нефтяной платформы
Thunder Horse PDQ является крупнейшей полупогруженной нефтедобывающей платформой в мире.
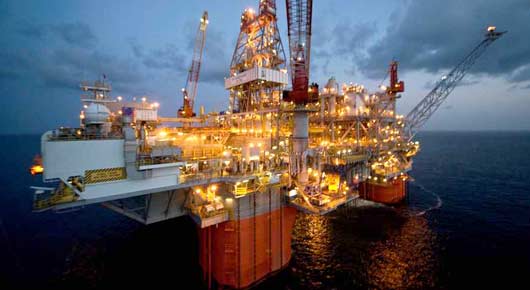
Затраты на строительство составили около пяти миллиардов долларов, а платформа, как ожидается, должна работать в течение 25 лет.
Thunder Horse PDQ была эвакуирована в связи с приближением урагана Dennis в июле 2005 года. После того, как ураган закончился, платформа сильно накренилась. Комиссия, которая осматривала платформу незадолго до этого, не обнаружила никаких нарушений целостности конструкции и рекомендовала отправить платформу на постоянное место работы.
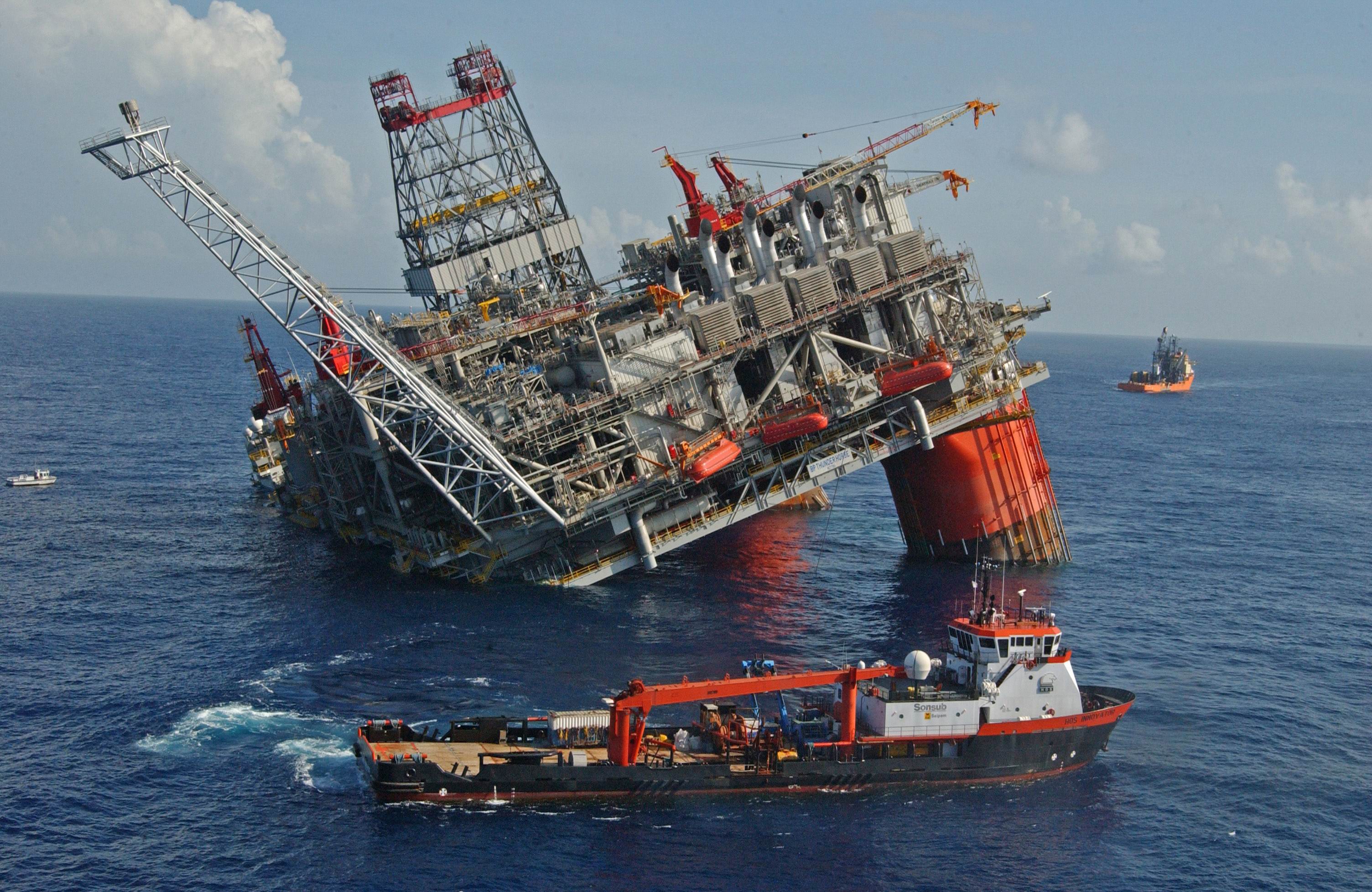
Thunder Horse после поломки
После осмотра платформы было выяснено, что трубы, которые вели к подводному коллектору оказались оторванными. Все трещины прошли по сварным швам, что и доказало, что причиной стало очень низкое их качество.
Главный инженер платформы Гордон Аакер отметил, что «такая поломка на месте добычи могла бы вызвать экологическую катастрофу»
Однако меньше чем через год платформа была полностью отремонтирована и вновь работала.